TOMSK, May 29 –
RIA Tomsk, Elena Taylasheva. One of the most
effective divisions of TPU to work with industry – Engineering School of
Non-Destructive Testing – is headed by the youngest at TPU school headmaster –
31-year-old Dmitry Sednev. How his team earned 340 million and how many times
you need to hear "no" before getting a contract – in the material of
RIA Tomsk.
To look deep
into
The world is
becoming more complicated, technology is becoming more sophisticated, industry
in its advanced areas is developing so rapidly that it requires completely new
approaches to security. For example, the rotor blades of advanced helicopters
are made of super strong and at the same time lightweight carbon fiber, but
before installing they must be checked: is there any delamination inside the
material?
Or – France is
implementing an international project to build the world's first thermonuclear
reactor. Not a single detail should have a hidden defect, otherwise it can fail
under load, which will lead to disastrous consequences. And these details, for
a minute, can be 1.5 tons weight each ...
Non-destructive
testing – is just an opportunity to look deep into an object without destroying
it. Dmitry Sednev shows a large transparent cube with a robot manipulator,
installed in one of the laboratories of the school, and explains how works one
of the most common methods of automated ultrasonic testing – immersion one.
© предоставлено Томским политехническим университетом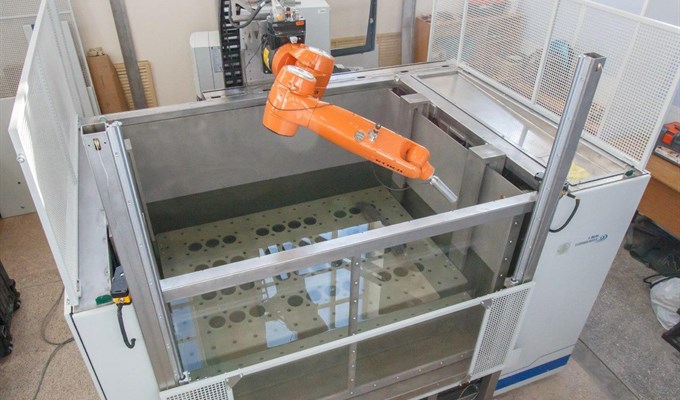
Bath for ultrasonic control
"A part to
be checked is placed in the water bath (water is a wonderful conductor, it does
not absorb ultrasonic waves). A control program is set, and a robot with an
ultrasonic transducer "rolls" along the surface of the object. The
resulting data array is processed using a mathematical algorithm developed by
us, and creates a three-dimensional model of the internal structure of the
product.
One can see the
shape of the defect (if any), its actual size. Compared to the traditional, "manual"
ultrasonic testing method, when the operator simply moves the sensor with the
gel along the surface of the part, this is a significant step forward", –
says Sednev.
Installation in
the laboratory allows to "see through" parts weighing up to half a
ton, and, for example, in the St. Petersburg Scientific Research Institute of
Electrophysical Apparatus (NIIEFA), polytechnics are now finishing debugging
operating modes for a modernized analogue that controls parts three times
harder. They are designed just for a fusion reactor in France, in particular,
NIIEFA is responsible for the systems that hold the plasma inside.
"If it were
not for the coronavirus, we would solemnly put the system into commercial
operation in April", – smiles Sednev.
© РИА Томск. Таисия Воронцова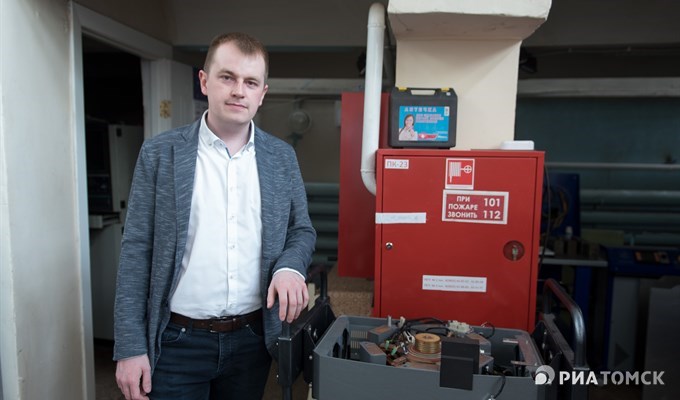
The history of non-destructive testing began at TPU in the 1950s with the production of betatrons – particle accelerators that form secondary X-rays (Large Hadron Collider in miniature). Inspection systems with a "heart" in the form of betatrons are able to transilluminate 350 mm steel.
Commercial case
Dmitry Sednev
came to the international non-destructive testing laboratory, founded at the
institute of the same name, in 2010, and was among its first employees. TPU
then won an open competition to attract leading scientists to Russian
universities, the laboratory was headed by professor Michael Kröning, the
director of the Fraunhofer Institute, a world "star" in this field.
"I was in my
fifth year at the Faculty of Physics and Technology, my research was not
directly related to non-destructive testing, but my research supervisor Dmitry
Georgievich Demyanuk proposed to work on this topic. We started developing a
technology for controlling containers with nuclear materials and waste for
Rosatom", – tells Sednev.
© предоставлено Томским политехническим университетом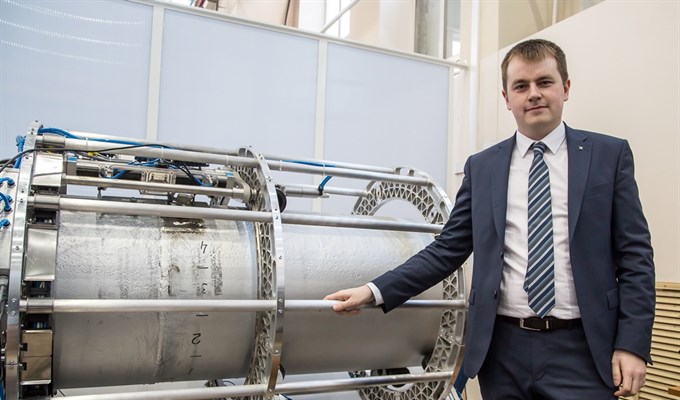
Ultrasonic tomograph for monitoring spent nuclear fuel storage cases.
The idea was
this: each container has "fingerprints" – welds, each of which is
unique. Having data on the initial state of the weld, it is possible to check
with the help of ultrasound inspection whether it was subjected to any
influences, whether someone tried to open the seam, and whether that is the
container at all. For this study Sednev received a scholarship from the
Presidential Program for Support Young Scientists.
In 2017, a young
scientist, at that time already the head of the non-destructive testing
laboratory, was invited to the position of the deputy director of the entire
school. Literally a month later, his head – Valery Borikov – had a stroke, and
Dmitry Sednev became "acting director".
Then Tomsk
Electromechanical Plant (TEMP) – a long-time partner of the Engineering School
of Non-Destructive Testing – worked on a gigantic project with Gazprom to
produce valves (gate valves) for the Power of Siberia gas pipeline. Gate valves
to control the gas flow in the pipe were supplied from abroad, mainly from
Holland. Tomsk citizens had to make a Russian analogue.
© предоставлено Томским политехническим университетом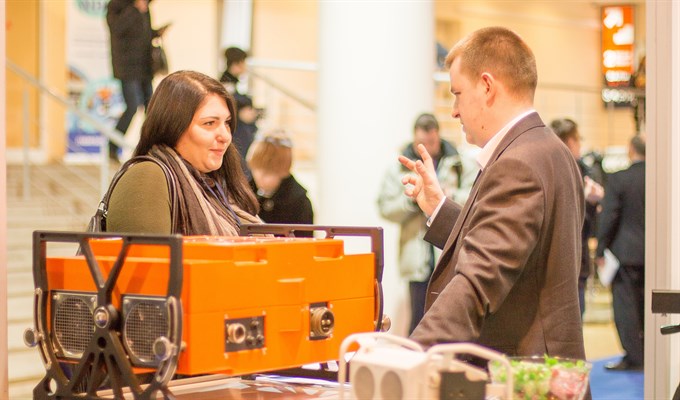
"There were always people nearby who knew more, did more, and I learned from them. When I headed the institute, I was 29 years old. Of course, not everyone was excited about it. But over time, I managed to establish trustful and respectful relations", – says Dmitry Sednev.
"At the start of
the project, Valery Nikolayevich (Borikov) came to the director of TEMP Ivan
Pushkarev and suggested to develop an intelligent system for non-destructive
testing – new products needed new control methods. The difficulty was that the
valves – are huge parts made from whole castings, up to 2.5 meters in diameter.
You can’t immerse them in any bath ...
Ivan Ivanovich
(Pushkarev) supported the idea. We wrote one grant application, didn’t win,
then we wrote the second one – to another program, and we received 150 million
rubles from the state (because the project was related to applied research),
and the same amount was invested by the plant itself", – Sednev said.
For three years,
polytechnic engineers (and the work involved "neighboring"
engineering schools of TPU – Computer Science & Robotics, Advanced
Manufacturing Technologies, Nuclear Science & Engineering) realized an idea
that no one in the world had thought of before. For the new control system, as
well as for the standard ultrasound examination, water was also needed, but not
in tons, but in the volume ... of one and a half liter bottle.
"The part
is placed in a specially designed acoustic path. A device is mounted on the
robot’s flange (end), in which, using additive technologies, are placed
channels for supplying water to a special material that does not dampen
ultrasound. Water is supplied through one channel and drawn back through the
other by compressed air, as a result of which there is no prolonged contact
with the product occur.
This, I believe,
is another breakthrough in non-destructive testing, because there are a lot of
materials that cannot be wetted – the same carbon fiber. I hope the project
will have its own separate glorious story", – says Sednev.
So, recently he
got a call from the Novosibirsk Institute of Nuclear Physics, which also
produce test equipment for a thermonuclear reactor in France, and the details
cannot be lowered into the bath. “Make us the same cool control system as for
the NIIEF, but without water", – they asked.
"I answer:
“Imagine, we already have one!". Two days later they come, I take them to TEMP,
they are surprised: "Can't the university do that!". Unfortunately, many
industrial partners are still in the consciousness that universities develop
well, but poorly implement: they say, we screw up with taptites that fall off,
then wrap it with blue electrical tape and deliver work to the customer with
the words: "If you do not breathe, it will work".
We have to break
this stereotype: we have a very high culture of modern technological
production. In general, I would call our team leaders in the field of custom
solutions for non-destructive testing all over the world. This is a good
strategy for the university: to set trends themselves instead of following
them, at least in two or three sectors", – Sednev emphasizes.
пресс-служба ТПУPolytechnics integrated the system for TEMP into the industrial process – a separate workshop was built to control parts. Now it works in test mode, it will be inaugurated in July.
Turnkey tasks
In 2019, TPU
Engineering School of Non-Destructive Testing earned 342 million rubles, this
is one of the most successful indicators in TPU. As for the specific output per
person, the School is the leader in the university – it is 4 million 160
thousand rubles per employee. The School is also the best in terms of business
contracts – in a year it completed them for 192 million.
This and next
year, Sednev hopes to further increase turnover: will begin a project with the
Institute of Nuclear Physics, will develop a cooperation with Cancer Research
Institute on the use of betatrons for cancer treatment, negotiations are
underway with Sukhoi design bureau, which needs a device to control engines "in
the field", as well as with a number of companies that need a "desktop"
tomograph.
© РИА Томск. Таисия Воронцова
"The work on a grant and the work on a contract are different in the measure of responsibility: when you work on a grant, the result – is research, but it can be unsuccessful. And when the industrial partner pays you, you must give out a ready-made solution that will work on time", – notes Sednev.
Sednev believes:
the university not only CAN earn money on engineering – it MUST do it!
"We must
take complex tasks and solve them on a turnkey basis; we must act as an
integrator of new solutions for the industry. Moreover, we need to look for industrial
partners ourselves, and not wait for them to come. And do not be afraid to be,
I'm sorry, buggered off", – he says.
He himself was
told to get lost countless times: "We come and say "Our system costs
10 million, and they reply: "We only have a million, goodbye". If you
knocked on a closed door once, they didn’t open you, you turned around and left
– this is not the right approach. If you clearly understand that the idea is
worthwhile, you should look for those doors that will open".